So stellen Sie Silikonteile her: DIY-Methoden vs. professionelles LSR-Spritzgießen?
Einführung
Ob Sie einen Prototyp entwickeln oder die Massenproduktion vorbereiten – die Wahl des richtigen Silikonherstellungsverfahrens hat erhebliche Auswirkungen auf Kosten, Qualität und Lieferzeit. Während DIY-Ansätze für einfache Projekte funktionieren, erfordern professionelle Silikonteile Präzisionstechnik und fortschrittliche Techniken wie Flüssigsilikon-Spritzguss (LSR).
In diesem Leitfaden vergleichen wir die DIY-Silikonformung mit der industriellen LSR-Herstellung – und erklären, warum die Partnerschaft mit einem Experten wie SiliconePlus überlegene Leistung, Haltbarkeit und Skalierbarkeit gewährleistet.
Können Sie Silikonteile zu Hause herstellen? (DIY-Methoden und Einschränkungen)
Viele Hobbybastler und Startups experimentieren mit Silikonguss (bei Raumtemperatur vulkanisierendes oder RTV-Silikon) für einfache Formen. Diese Methode ist zwar kostengünstig, hat aber entscheidende Nachteile:
Geringe Präzision (±1 mm Toleranz gegenüber ±0,05 mm beim LSR-Formen).
Geringe Haltbarkeit – Anfällig für Risse, UV-Abbau und Hitzeversagen.
Eingeschränkte Skalierbarkeit – Handgegossene Formen können nicht mit der Geschwindigkeit einer automatisierten Produktion mithalten.
Beispiel: Ein handgegossenes Silikonarmband kann 6 Monate halten, während ein mit LSR gespritztes Band jahrelang Schweiß, Sonnenlicht und Dehnung standhält.
Wann wird man Profi?
Wenn Ihr Projekt Folgendes erfordert:
✔ Medizin-/Lebensmittelkonformität (FDA, ISO 10993)
✔ Komplexe Geometrien (dünne Wände, Hinterschnitte)
✔ Großserienproduktion (über 10.000 Teile)
—LSR-Spritzguss ist die einzige praktikable Lösung.
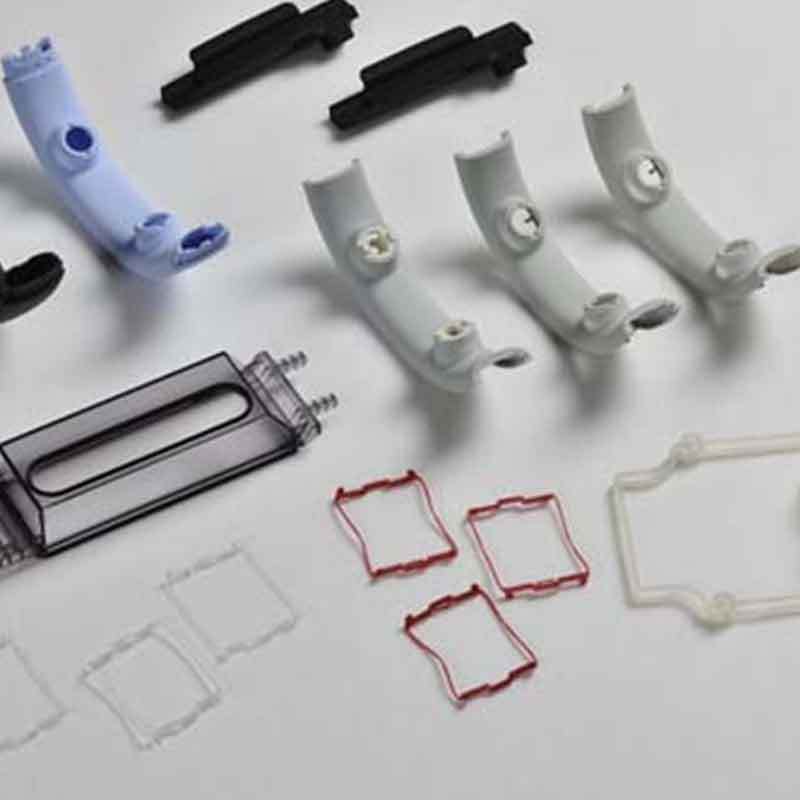
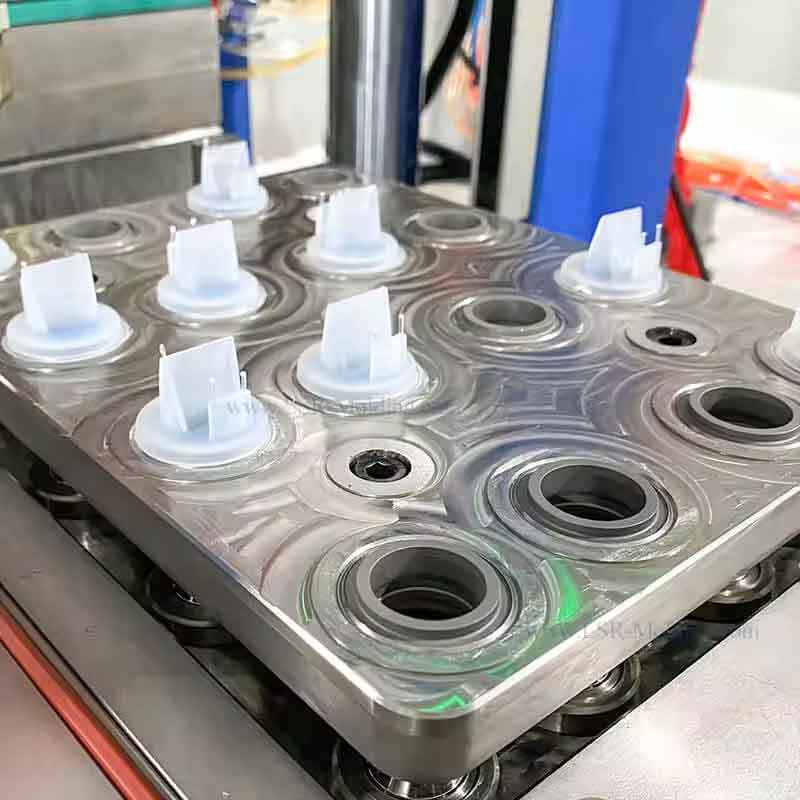
Wie SiliconePlus Hochleistungs-Silikonteile herstellt
Als führender Hersteller kundenspezifischer Silikonteile kombinieren wir Materialwissenschaft, Präzisionswerkzeuge und automatisierte LSR-Injektion, um Folgendes zu liefern:
Schritt 1: Materialauswahl
Medizinisches LSR (FDA, USP Klasse VI) für Implantate/Wearables.
Wärmeleitfähige Silikone für die Elektronik.
Shore-Härte 10A–80A (ultraweich bis starr).
Schritt 2: Formenbau und Werkzeugbau
Formen aus gehärtetem Stahl (Lebensdauer über 50.000 Zyklen).
Mehrfachkavitätenformen zur Reduzierung der Stückkosten.
3D-gedruckte Prototypen zur Designvalidierung.
Schritt 3: LSR-Injektionsprozess
Vollautomatische Pressen mit einer Wiederholgenauigkeit von ±0,02 mm.
Gratloses Formen für keine Nachbearbeitung.
Umspritzen (z. B. Silikon + Kunststoff/Glas).
Schritt 4: Qualitätssicherung
100 % Maßprüfung (KMG-Maschinen).
Zug-/Reißprüfung gemäß ASTM D412.
Sterilisationsvalidierung (Autoklav, ETO, Gamma).
Warum sollten Sie SiliconePlus für Ihr Projekt wählen?
✅ 72-Stunden-Prototypen – Beschleunigen Sie Ihre Forschung und Entwicklung.
✅ Zertifiziert nach ISO 13485 und ISO 9001 – Medizinische/industrielle Konformität garantiert.
✅ End-to-End-Support – Von der DFM-Analyse bis zur Logistik.
Angebot für eine kostenlose Designprüfung:
Senden Sie Ihre CAD-Datei für eine kostenlose Herstellbarkeitsprüfung und ein Angebot innerhalb von 24 Stunden.
Häufig gestellte Fragen
F: Wie viel kostet eine individuelle Silikonform?
A: Von 2.000 (einfache Designs) bis 2.000 (einfache Designs) bis 20.000+ (Mehrfachhohlräume, Mikromerkmale).
F: Können Sie Pantone-Farben anpassen?
A: Ja – Wir unterstützen benutzerdefinierte Pigmente und durchscheinende/undurchsichtige Oberflächen.
F: Was ist die Mindestbestellmenge für LSR-Teile?
A: Schon ab 500 Stück für Produktionsläufe.